檢驗員就是產(chǎn)品質(zhì)量的“守門員”
檢驗員就是產(chǎn)品質(zhì)量的“守門員”
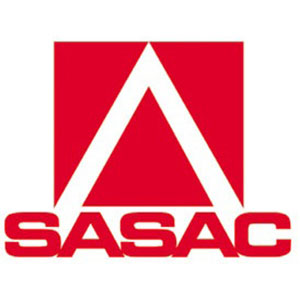
文章來源:中國航天科工集團有限公司 發(fā)布時間:2018-06-27
“現(xiàn)在,檢驗人員能主動到車間巡檢,我們車間交驗產(chǎn)品不需要再到樓上找檢驗員了。”這點,生產(chǎn)一線員工感受頗深,“以前,我們要打電話,他們才下來。”一年來,航天晨光化機分公司檢驗組在組長臧正海的帶領(lǐng)下,從改變檢驗作風(fēng)提高服務(wù)質(zhì)量入手,部門形象正悄然發(fā)生轉(zhuǎn)變。
2018年,化機分公司訂單增加產(chǎn)出壓力加大,為趕進度保交貨,從4月開始,分公司組織開展第一階段勞動競賽活動,車間每天加班加點,形成多場景多工位多班制的生產(chǎn)組織方式,快節(jié)奏的生產(chǎn)壓力和當(dāng)下檢驗人員緊缺的現(xiàn)狀,對分公司來說無疑是一個巨大考驗。臧正海作為檢驗組組長主動擔(dān)當(dāng)起了三個車間產(chǎn)品的檢驗任務(wù),積極配合檢驗機構(gòu)的調(diào)整和整合,在組織變動的過程中,合理調(diào)配檢驗資源,主動補缺,變被動交檢為主動交檢,很好的保障了生產(chǎn)進度和質(zhì)量。
作為檢驗組組長,臧正海在努力提高自己技能水平的同時,還注重提高每位檢驗人員獨立開展過程檢驗的能力。2017年,分公司接到兩臺出口壓力容器產(chǎn)品的任務(wù),業(yè)主對產(chǎn)品層板間隙提出了非常高的要求,要求層板間隙控制在0.8mm以內(nèi),這個數(shù)據(jù)十分重要,是保證多層包扎容器最終承壓能力和承受疲勞載荷能力的關(guān)鍵指標(biāo)。為此,分公司配備了間隙檢驗尺,對于這個特殊檢驗方法,臧正海召集產(chǎn)品專職檢驗員,指導(dǎo)他們?nèi)绾握_使用間隙尺,還專門制作了層板間隙檢驗記錄表格,表格對縱環(huán)縫間隙的方位、弧長、高度、間隙面積都做了詳細記錄。單臺設(shè)備僅各層間隙檢測數(shù)據(jù)近千個,檢驗員依據(jù)這個表格在現(xiàn)場邊包扎、邊測量、邊記錄,全力配合業(yè)主代表的監(jiān)造,對生產(chǎn)過程中出現(xiàn)的問題做到及時發(fā)現(xiàn)、及時溝通、及時協(xié)助解決,確保了層板間隙關(guān)鍵指標(biāo)驗收一次性通過。通過此項目的實施,分公司層板的組裝形成了一個實用的檢驗記錄模板,有效的控制此類產(chǎn)品的包扎質(zhì)量。
2018年4月初,用戶要求提前交付某石化項目的一臺高壓汽包產(chǎn)品,該產(chǎn)品焊接前要求進行預(yù)熱,焊后還需消氫處理,加上此設(shè)備上共有52個接管,全部是要求全焊透的角焊縫,焊接工作量很大,檢驗工作要做到既保證質(zhì)量又不耽誤生產(chǎn)進度。為了做好質(zhì)量管控,減少返修對交貨期的影響,每天一上班,臧正海就趕去現(xiàn)場進行質(zhì)量監(jiān)控,確認焊接預(yù)熱溫度是否符合要求,對逐個焊條筒查看,確認焊條加溫情況,對照工藝卡,檢查焊接線流量,把預(yù)防和控制前置。由于控制到位,分公司按用戶要求完成了任務(wù),為公司贏得了信譽。
2018年1至5月,在臧正海和檢驗團隊的共同努力下,通過扎實開展質(zhì)量提升活動,分公司焊縫探傷一次合格率提高到96.22%,出廠產(chǎn)品返修率為0,過程中未出現(xiàn)批次性質(zhì)量問題。“100個檢驗要素,99個我們做到了,1個出現(xiàn)偏差也是失職。”他是這么說也是這樣做的,他清楚自己和團隊背負著沉甸甸的責(zé)任。
【責(zé)任編輯:李巨堯】